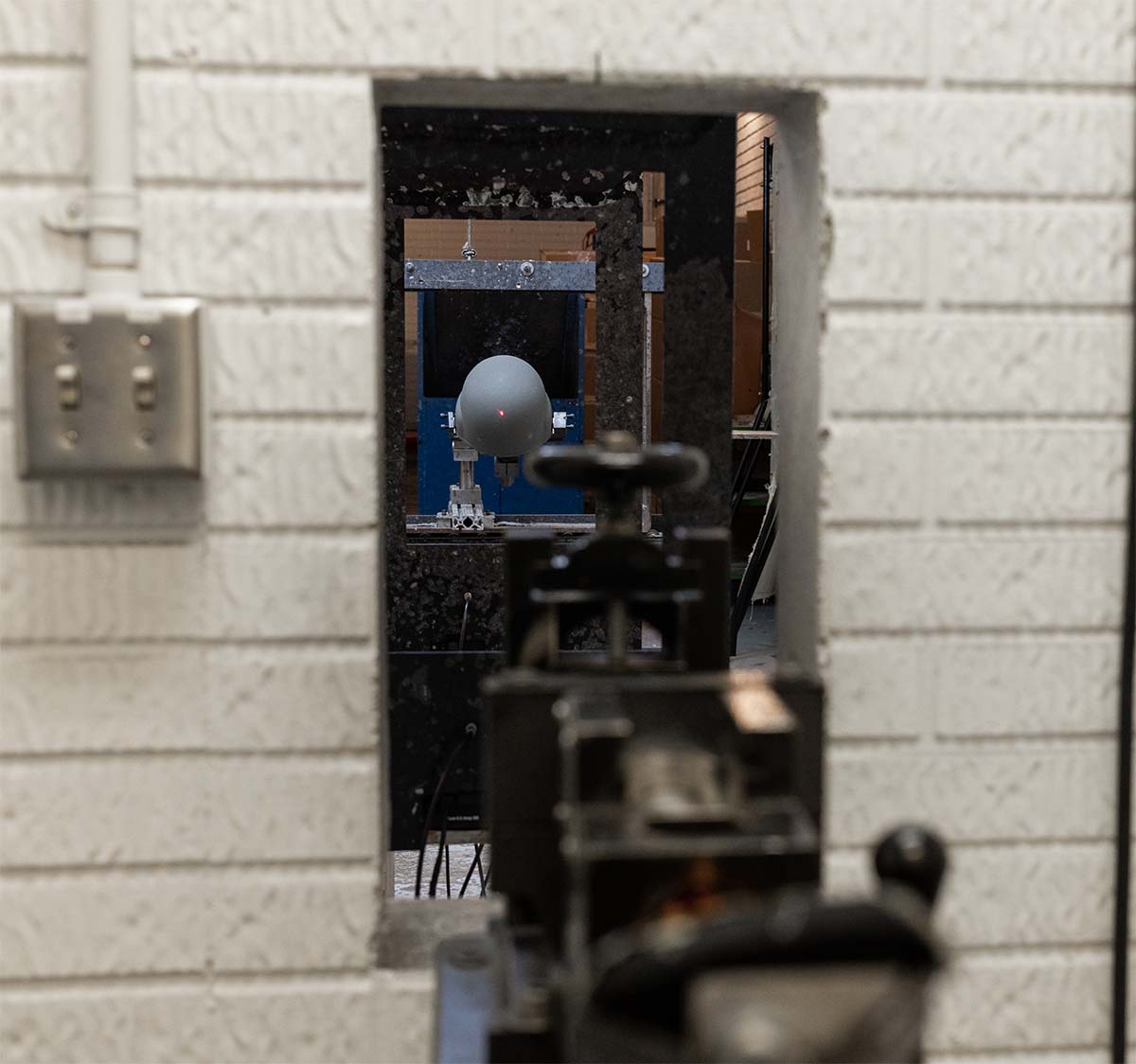
RESEARCH AND DEVELOPMENT
Developing Life Saving Head Protection Solutions
As a global leader of advanced ballistic head protection solutions and a product developer for the United States Government, ArmorSource employs a highly skilled Research and Development team composed of industry leading professionals. Since 2005 we’ve lead the industry in developing, designing and delivering innovative ballistic helmet solutions that incorporate bullet-resistant safety standards, customized sizing, ergonomic lightweight comfort, and technical functionality specifically built for military and law enforcement
operations around the globe.
Our R&D team benefits from an extensive array of testing equipment including a state-of-the-art in-house ballistic and non-ballistic testing lab, as well as
expertise and insight from modern day field operators who provide real-life practical feedback and knowledge.
Working alongside industry leading ballistic material manufacturers, our engineers have extensive composite materials expertise as well as a deep knowledge of composite processing technologies. ArmorSource maintains special relationships and teaming agreements with key materials suppliers and manufacturers of specialty helmet accessories such as mounts, rails, and harnesses to ensure state of the art technology remains the baseline at ArmorSource.
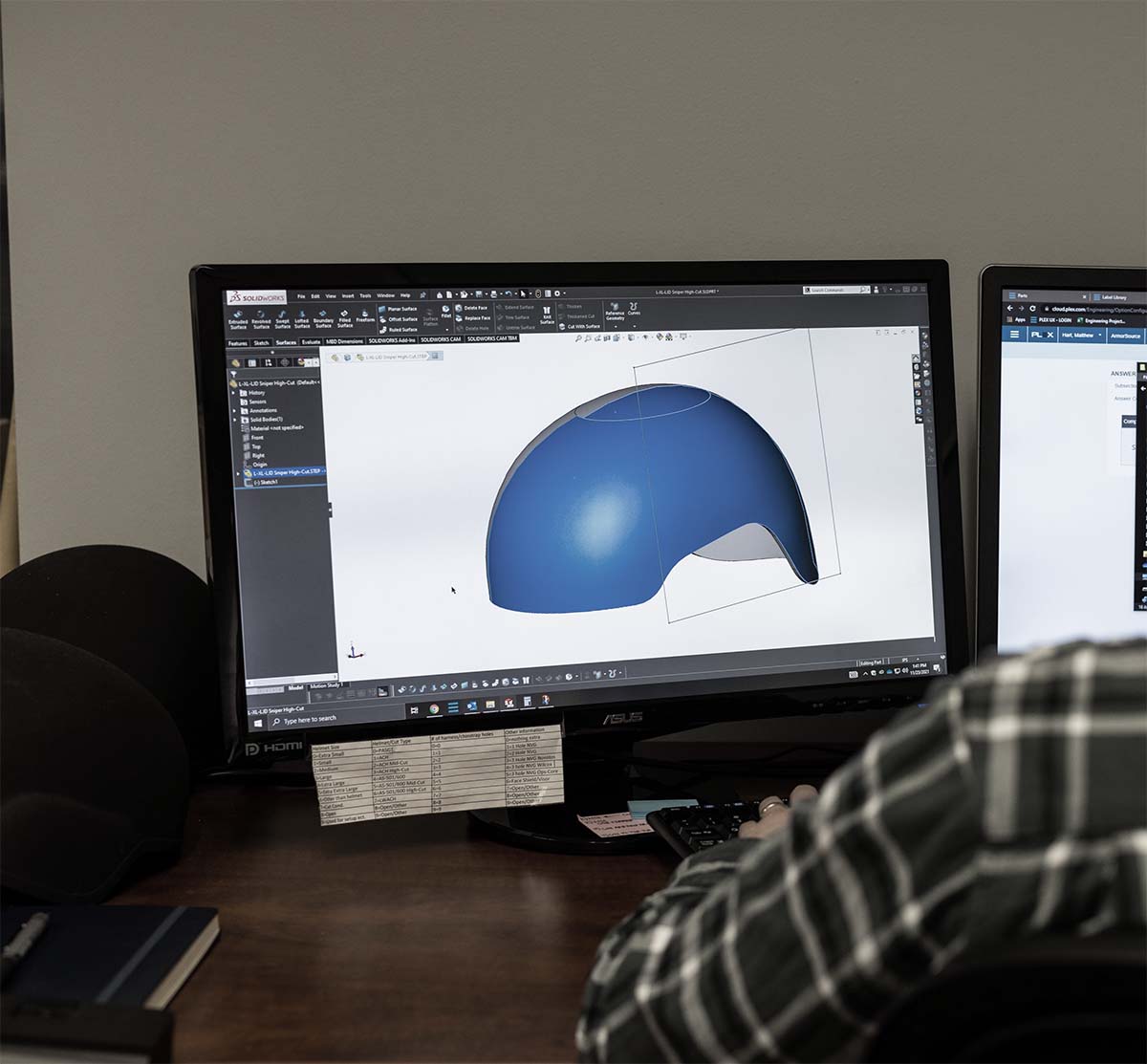
PRODUCT DESIGN
The Art of Ballistic Product Design
The success of a Ballistic Helmet design hinges on how well it can accommodate the ever-changing needs faced by soldiers and law enforcement agents in action. The threats they face evolve daily and so too must the solutions we provide. In its simplest form, our goal is to design helmets that protect the operator’s head from injury, and to increase their rate of survivability.
At ArmorSource we believe product design is an artform. We transform proprietary fabrics into rugged ballistic barriers designed to save lives. In doing so our team of industry leading product designers are tasked with managing unique needs, environments, weather conditions, threats, specific client requirements and most importantly – operator confidence.
Our designers are constantly looking for ways to trim weight, increase ballistic performance, improve comfort, deliver industry changing product, and ultimately set the standard for the ballistics industry worldwide.
In doing so, we focus on 3 key elements of design.
Protection
Our first mission is to protect our users against ballistic, environmental and mechanical threats. Each of our shells are designed to meet or exceed specific levels of protection mandated by our customers, such as the impact and effects from different rounds, fragments or mechanical threats.
Weight
Making sure our helmets perform at the highest level possible under extreme environmental conditions is a baseline requirement at ArmorSource. We’ve put it upon ourselves to design helmets that uphold these performance metrics but with significantly lighter areal density than our competition.
Customization
Designing helmets that provide maximum ballistic protection with decreased overall weight is what we do. But our products will only be considered mission ready when they deliver specific characteristics and capabilities required to support the unique needs of our customers. ArmorSource products are always designed to serve the user in the most ergonomic way, with the highest level of compatibility for common accessories, apps and add-ons making each helmet the perfect platform for the mission at hand.

TESTING
Tested. Proven. Trusted.
Safety. Reliability. Protection. Confidence. These are the promises ArmorSource aims to deliver. In an ongoing effort to improve the quality and safety of our products, and to ensure the development of new technologies ArmorSource leverages our on-site, state-of-the-art ballistic and non-ballistic testing labs to deliver convenient, time-sensitive testing against various ballistic, environmental, and mechanical requirements.
Our testing labs replicate real-life threats, similar testing facilities and methods of our customers, and meet the standard requirements set for independent commercial labs. Our ballistic range provides a safe and controlled environment for testing handguns, fragments (Right Circular Cylinder, Fragment Simulating Projectiles – 2, 4 ,16, 64, 17 grain), small arms (rifles), and back-face deformation (trauma).
Additionally, our in-house testing capabilities include environmental and mechanical testing which allows us to evaluate and deliver optimal performance characteristics, such as blunt impact, compression resistance, impact resistance, helmet stability and additional safety features for every helmet we produce.
To support the most demanding users on the planet and to ensure confidence in product, our quality assurance team leverages state of the art testing capabilities to ensure that every product that leaves our doors will meet or exceed required performance metrics.
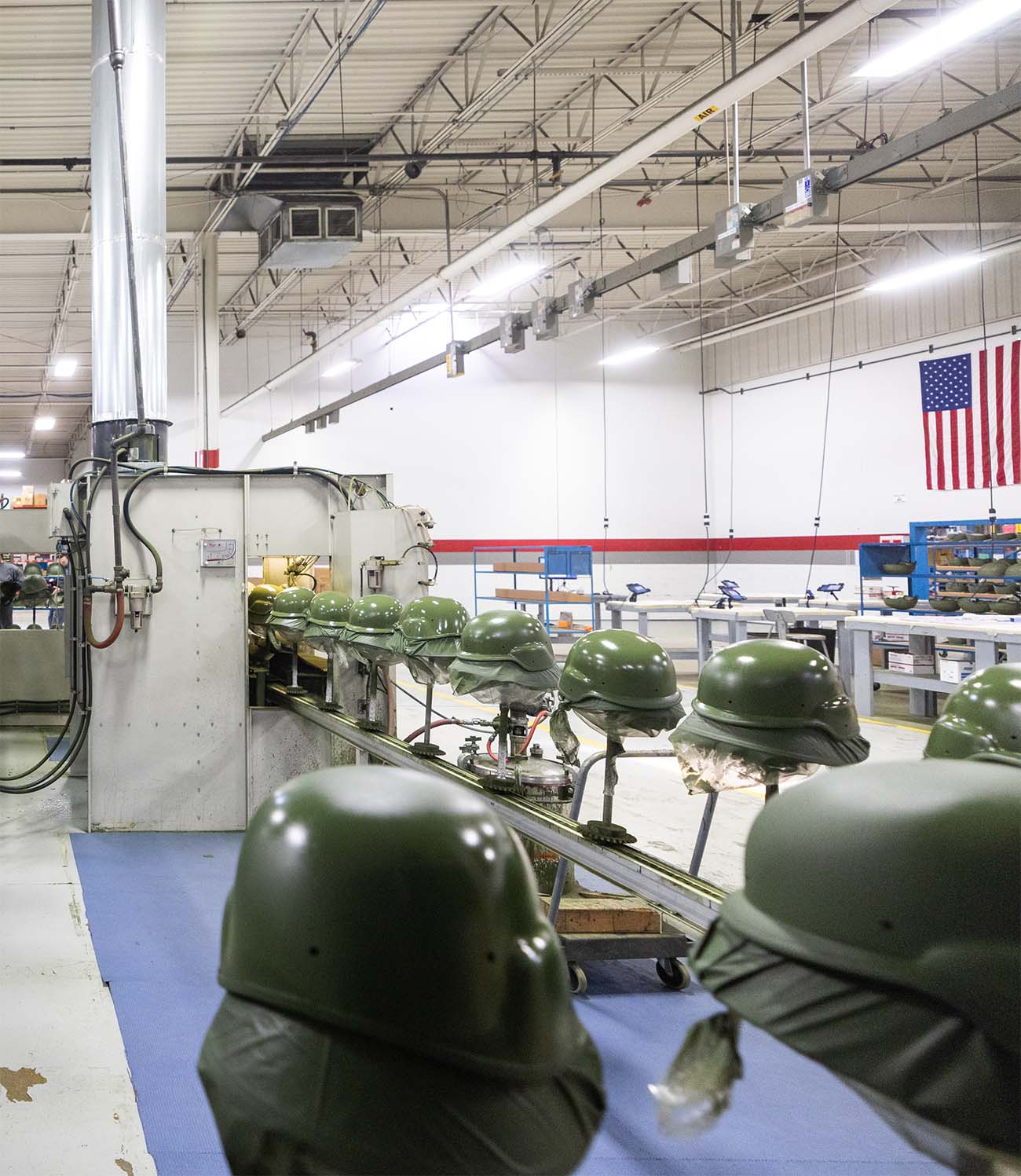
MANUFACTURING
A Global Leader in Custom Ballistics Manufacturing.
Our team is poised and ready to support your needs. Located in Hebron, Ohio, ArmorSource has one of largest helmet production facilities in the world. Our 120,000 sq. ft (11,000 sqm) facility is dedicated to the design, manufacturing and development of ballistic materials and custom ballistic headborne protection systems. ArmorSource is capable of building an estimated 30,000 aramid fabric based phenolic – PVB resin shells or 12,000 Polyethylene based shells per month.
Our production team operates and maintains a wide variety of automated, semi-automated, and manual machinery in a streamlined production environment. Our main production capabilities are:
• Automated Computer controlled cutting machines
• Pre-mold cold press machines
• Pneumatic hot press machines
• Six axis laser cutters
• Automatic paint booths
ArmorSource’s state of the art production facility is critical to achieving greater productivity, efficiency, and sustainability for our customers specific needs. We excel when the challenge and demands increase, and we strive to surpass expectation thanks in large part to process controls and automation technologies that enable us to maximize the productivity of our equipment for military and law enforcement organizations around the globe.
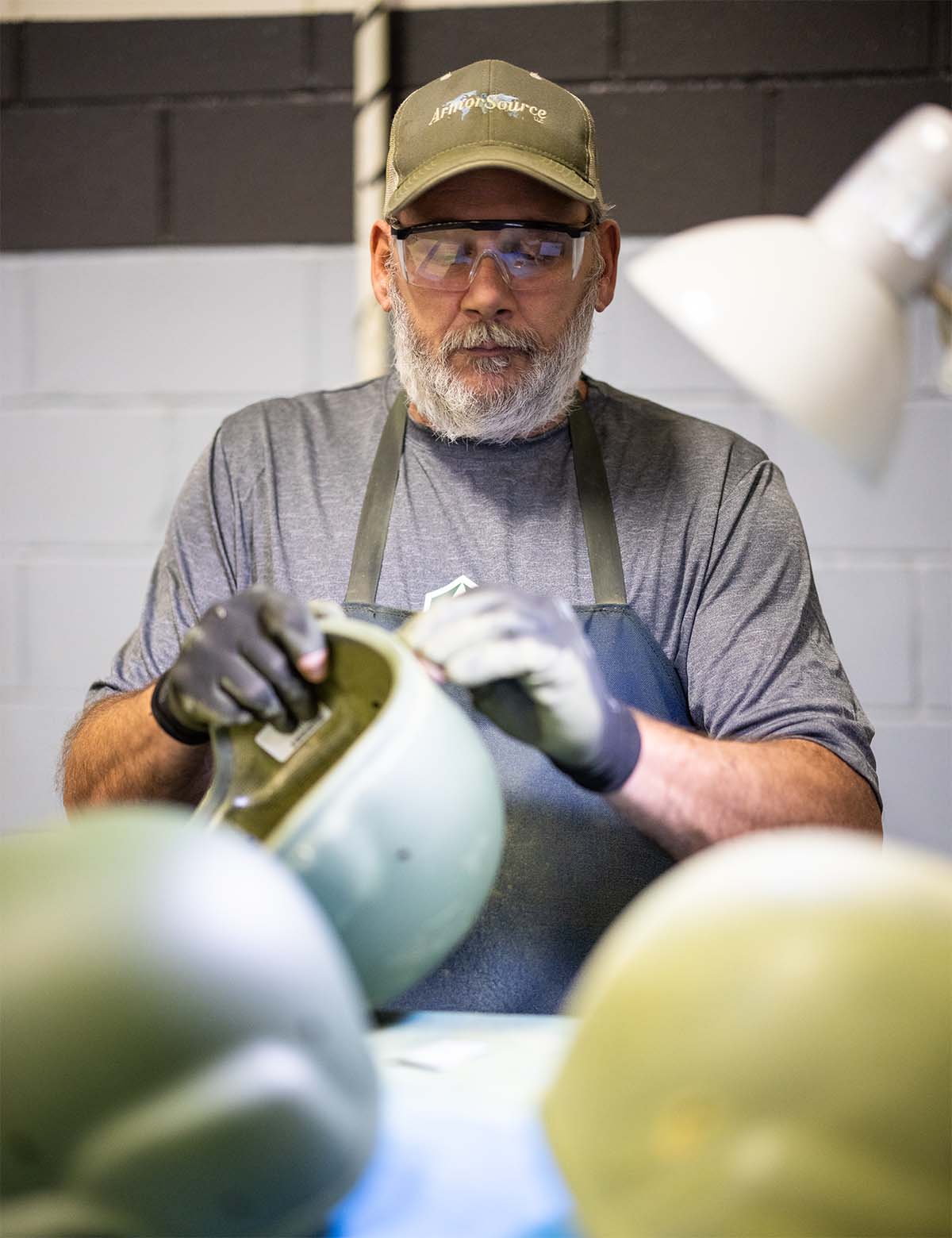
QUALITY ASSURANCE
Committed to exceeding standards and expectations.
ArmorSource’s commitment to quality is key to our continued leadership in a highly competitive global marketplace. Our continued growth and improvement of products and processes allows ArmorSource to meet and exceed our customers’ requirements.
Our certified Quality Assurance (QA) system is designed to meet the requirements of our customers effectively and efficiently. The Quality Manual, detailed processes, and work instructions that make up our Quality Management System are based on the requirements of ISO 9001:2015 and applied to each-and-every customer. Additionally, ArmorSource meets the requirements of AQAP 2110 when required by customer contract. We ensure all personnel follow the established QA process, applicable quality directions, and Government specifications and requirements.
ArmorSource’s quality program recognizes the unconditional requirements set forth by our customers, industry partners, and employees. As a company we understand their needs and we strive to meet or exceed expectations with unquestioned integrity and the highest quality of products and services.
During the production cycle, all task teams and individual task members are responsible for the quality of the product they receive from the task member ahead of them. This level of responsibility empowers task teams and individuals with the authority to take a broad range of initiatives to ensure 100% customer satisfaction so that the quality built into our products is proven by the quality seen and the quality tested.
Our approach to quality assurance/control and customer satisfaction is to integrate QA activities into the planning and execution of every task throughout the production cycle, which allows us to avoid dependency on final inspections. This approach allows problems, deficiencies, or necessary corrective action to be taken immediately at any step in the process, eliminating the need for costly and time-consuming rework.